Tech Targets Construction Risk Management
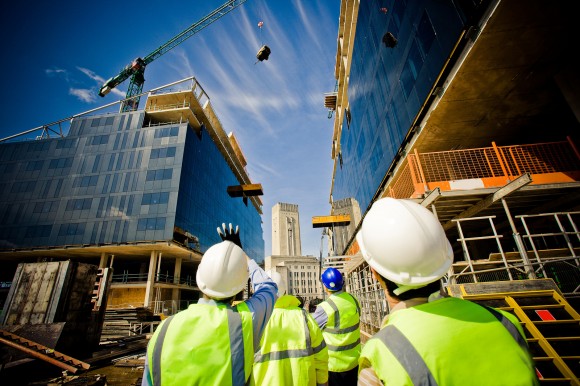
Water sensors that detect leaks before a lot of damage is done, wearables that track workers’ whereabouts and video cameras that monitor sites — the building industry is gradually adopting these and other technologies to help it improve safety and operations.
In the near future, construction firms are likely to be deploying robot bricklayers for simple jobs, fitting workers with exoskeletons that reduce physical strain, and training laborers by simulating building scenarios using virtual reality, according to insurance specialists in the field.
The construction industry is counting on technology to help it address its labor shortage and the safety of its workers, as well as improve its property risk management and overall efficiency.
Contractors are continually looking for new and better ways of doing work, according to Linda Stueber, Nationwide’s vice president of construction for standard commercial.
In her 25-plus years working in construction, previously as construction and operations leader for Travelers Southern and Midwest regions for Travelers, Stueber has found contractors to be early adopters of technology.
She points to the wearables as an example of a technology she believes the industry was quick to adopt and which shows great promise to improve both safety and productivity.
Construction industry wearables include high-tech vests and helmets that have lights or vibrate to alert employees of potentially dangerous changes in surroundings. Wearables can monitor employee movements and alert coworkers of danger, as well as monitor fatigue, body temperature and repetitive motion.
“There are many reasons a contractor would use wearables but an important reason is to track where your employees are located. That can be very beneficial from a safety perspective,” Stueber said.
Jim Marquet, managing director at The Graham Company, an independent insurance brokerage and consulting firm based in Philadelphia, said wearables are helping to curb falls and injuries from being hit or struck by heavy equipment, which are a main loss issue on construction sites. This technology is helping to prevent the “nightmare scenario” of the general contractor that has a worker on the job site who is injured and then left unattended.
“As it relates to falls, there is new wearable technology that provides the ability for a general contractor or a trade contractor to track the location of employees in real time to identify where they are. If they’ve fallen or if something’s fallen on them the sensor has the ability to report that (accident) in real time,” Marquet said. The ability to track where workers are at any time helps protect workers from entering into areas of a construction site deemed unsafe as well. “Plus, in an event of an investigation after the fact it’s easy to identify who was in a given area and really track what they are doing,” he said.
Steve Lako, vice president of loss control at Allied World, specializing in working with construction companies, says wearables can keep workers from going into unsafe areas. Even when workers are trained properly with site walk-throughs and safety training meetings, there’s always a chance that someone might wander into an unsafe area or hot zones.
“We are seeing a real benefit from a safety standpoint,” Lako said. “For instance, you can map out all the critical safety zones of a project and store it in some type of software app or building information management system. With that information you can then, through wearables, have warning signals given to your employees when they enter into different hot zones or safety zones. Those warnings can be in the way of an audible device, or lighted signal.”
Wearables also play a role in monitoring the vital signs of employees. GPS technology in wearable vests can locate the injured worker, which may be critical for emergency response.
Not all the technology is wearable. Building firms also see promise in using site sensors to protect workers. Companies like SmartSite and Pillar Technologies have developed site sensors that can be deployed across a construction site to monitor temperature, noise levels, dust particulates and volatile organic compounds to help limit workers’ exposure to these dangers. The sensors collect data that can analyzed so that owners can mitigate exposure levels and stay compliant with OSHA regulations.
High Tech Sensors
In addition to being used to protect workers, technology is being used to protect property. Water and fire sensors along with video guards are proving to be popular risk management tools on construction sites.
Technical Risk Underwriters (TRU), a specialty underwriter of insurance products for complex property and construction risks based in Austin, Texas, worked with Fedora Security, a Texas-based security solutions provider, to develop an ultrasonic device that detects after-hours water flow in water main and sprinkler pipes and alerts a security monitoring station in real time when a sensor is triggered.
In addition to waterflow monitoring, TRU is relying on Fedora for electronic surveillance using video analytics. The technology does not require a guard to view a monitor but instead the software triggers an alert when it detects a certain kind of movement within a predefined perimeter including flames from a fire.
“A very important issue for us is protecting a property after hours,” said Mike Pilla, CEO of TRU, a division of RSG Underwriting Managers. “There’s been five $50 million fires (on construction sites) during the first half of this year alone that are deemed as suspicious fires that happened after hours.”
While most large construction sites employ watchman/guards, more needs to be done to provide sufficient protection, according to Pilla. “We’ve learned watchmen on big construction sites are relatively ineffective.”
TRU has video evidence it says backs up that claim. “We have video of real examples of watchman failing,” said Michael Souery, chief operating officer and chief analytics officer of TRU. “We have quite a few (construction) sites where the insured chooses to have both watchman and the electronic surveillance and in all incidents, the electronic security is the one intercepting the intrusions rather than the guard. We’ve witnessed a case where the operator (electronic surveillance) remotely challenged the intruders who ran away passing a parked car where the guard appeared to be sleeping and missing all the action.”
It’s a common situation, Souery added. “You can’t rely totally on the guard. Even if they are doing their job well it’s not feasible to have a guard walk every 20 minutes around a large site which could be two or three blocks long.”
This is why Souery and Pilla say a combination of technology and human intervention is the best bet to managing fire and water risk on construction sites today. They feel so strongly about its effectiveness that TRU mandates use of Fedora’s Modular Integrated Protection & Surveillance Solutions (MIPSS) technology, that detects and alerts for intrusion, vandalism, theft, fire and flood at construction sites, on all construction accounts of a certain size.
“Imagine a site shutting down on a Friday night then a plumbing fixture fails on the fourth floor. The contractor shows up on Monday morning to find three or four floors of a building damaged,” Pilla said. “Oftentimes those are seven figure losses. Technology could have detected the water and mitigated the severity of the loss.”
Pilla says that he’s not aware of any other broker using Fedora’s technology today. “It’s something they’ve done exclusively for us.”
Robots, Exoskeletons and Virtual Reality
Robots show promise for the future, although thus far there hasn’t been much real use for them.
One highly publicized construction robot is SAM100 (Semi-Automated Mason). SAM is a robotic bricklayer launched in 2015 at World of Concrete. The enhanced version of the robot, Sam100 OS 2.0, which debuted in January 2017 at World of Concrete, is a much faster big brother of SAM100.
SAM was created by New York-based Construction Robotics, and can lay up to 3,000 bricks per day, with the help of its conveyor belt, robotic arm, and concrete pump. By comparison, a human can lay about 500 bricks per day. While SAM doesn’t come cheap (about $500,000), it’s seen as a potentially transformative tool in revolutionizing future building sites.
Robotic bricklayers aren’t yet seen as a realistic option to human masons, according to The Graham Company’s Marquet.
“Right now, the use of that technology is very limited,” Marquet said. A robot bricklayer can only lay bricks on straight runs, unlike a quality mason who can handle more complex jobs.
“It can’t do the difficult parts of a job. Frankly, a real mason is probably more productive than a machine,” Marquet said.
Even so, Marquet is aware that each year is likely to bring about advances in robotics.
Nationwide’s Stueber does see one advantage to SAM: it could reduce injuries.
“Bricklaying is some of the hardest and dirtiest work you can do on a construction job site and it’s prone to a lot of material handling injuries, too,” she said. “You don’t have to worry about back injuries on a robot.”
Exoskeletons may also be found on future construction sites. Exoskeletons? Think “Aliens” and Sigourney Weaver circa 1985.
Exoskeletons are wearable devices that work in tandem with the human user and are powered by a combination of technologies and mechanical equipment.
Today, exoskeletons and power-assist suits are being developed for industrial use so workers can lift and carry objects or use heavy tools for longer periods of time without putting undue stress and strain on the body.
Allied World’s Lako hasn’t yet seen an exoskeleton on a construction site but that doesn’t mean they aren’t coming.
One example where an exoskeleton might be used in construction is helping workers extend the time they can safely operate heavy machinery such as a jackhammer, he said. “If you add an exoskeleton to a human for jackhammer use theoretically that worker could go from being able to operate the jackhammer much longer without the fatigue typically associated with its use,” Lako said.
Virtual reality safety training programs offer another way to manage construction risk. Suffolk Construction, the largest U.S. construction company, which is based in Boston, Mass., envisions a virtual reality program where workers could walk through a jobsite and be presented with a scenario in which the worker must point out all the possible hidden dangers, such as live wires, misplaced ladders or a worker cutting a small piece of steel without wearing his protective goggles. Or if a real accident occurs on the job, the scenario could be recreated virtually to teach workers how to avoid the same mistake twice.
“I’ve seen it being used in crane safety (programs) to simulate hazardous areas – you can simulate a scenario and test actual procedures used in that process,” Lako said. Right now, only the large firms use virtual reality but it’s another area that could lead to safer construction sites.
But there is no guarantee a particular technology will be widely adopted by any industry. Remember Google Glass? It was once the next big thing and, while it remains in use in some industrial applications, it has not achieved widespread adoption.
Strongest Impact
In Lako’s view, the strongest impact on safety has not come from expensive technologies but from everyday mobile devices like smart phones. Insureds are using mobile devices to identify hazards in real time and share with others.
“It’s taking the idea of safety management and putting it in the hands of all employees not just a designated safety person a job site,” he said.
“It’s part of a whole overall idea that everyone is responsible for a safety culture. The only way to be truly safe is to have everyone engaged. Mobile devices are making that possible,” said Lako.
One downside to new developments in technology is a false sense of security that comes with implementing these high-tech tools on construction sites, especially as it relates to safety and risk management, said The Graham Company’s Marquet.
“I think the downside of it is to think that technology is some kind of panacea. ‘If we just have these sensors everything will be OK,'” he said. “The fact of the matter is that the human element will continue and as long as we have people building buildings — which is going to be forever — that will be an important part of it.”
Overall, the construction industry has become more sophisticated and more aware of how to improve its culture of safety, noted Robert Harris, vice president at Nashville’s The Crichton Group, middle Tennessee’s largest independent insurance agency. That focus on safety has led to better performance as well.
“2016 was a record year for contractors in the Nashville area and 2017 is going to be another record year,” he said. There’s no reason to expect a slowdown. “The biggest issue for contractors continues to be labor shortages.”
Perhaps technology will help.